سوراخکاری یکی از فرآیندهای مهم و پرکاربرد در تولید و مهندسی مکانیک است که به وسیله آن، سوراخهایی با اشکال و اندازههای مختلف در مواد مختلف ایجاد میشود. این فرآیند با استفاده از ابزارهای مخصوصی مانند متهها انجام میگیرد. هدف اصلی سوراخکاری ایجاد حفرهها یا سوراخهای دقیق و با کیفیت است که ممکن است برای مقاصد مختلفی مانند مونتاژ قطعات، نصب اتصالات یا عبور دادن سیمها و کابلها مورد استفاده قرار گیرد.
انواع سوراخکاری
سوراخکاری شامل انواع مختلفی است که هر کدام برای کاربردهای خاصی مناسب هستند:
۱-سوراخکاری معمولی (Drilling): استفاده از متههای پیچشی برای ایجاد سوراخهای ساده در مواد مختلف.
۲-سوراخکاری عمیق (Deep Hole Drilling): ایجاد سوراخهایی با عمق زیاد نسبت به قطر آنها، معمولاً برای قطعاتی که نیاز به کانالهای داخلی دارند.
۳-ریز سوراخکاری (Micro Drilling): ایجاد سوراخهای بسیار کوچک با قطر کمتر از ۱ میلیمتر، معمولاً در صنایع الکترونیک و پزشکی.
۴-سوراخکاری زاویهدار (Angle Drilling): ایجاد سوراخهای با زاویه خاص نسبت به سطح کار، مورد استفاده در قطعات پیچیدهتر.
۵-سوراخکاری پلهای (Step Drilling): ایجاد سوراخهای با قطرهای مختلف در یک عملیات، که به تدریج بزرگتر میشوند.
صدور پیشفاکتور آنلاین
ابزارهای سوراخکاری
برای انجام عملیات سوراخکاری، ابزارهای مختلفی به کار میروند:
- متههای پیچشی (Twist Drills): رایجترین نوع مته که برای ایجاد سوراخهای ساده و معمولی استفاده میشود.
- متههای کاربیدی (Carbide Drills): برای سوراخکاری مواد سختتر مانند فولادهای سخت و مواد کامپوزیتی استفاده میشود.
- متههای تفنگی (Gun Drills): برای سوراخکاری عمیق و دقیق.
- متههای پلهای (Step Drills): برای ایجاد سوراخهای با قطرهای مختلف در یک عملیات.
ماشینآلات سوراخکاری
ماشینآلات مختلفی برای انجام عملیات سوراخکاری وجود دارند، که از جمله میتوان به موارد زیر اشاره کرد:
- دریلهای دستی (Hand Drills): ابزارهای قابل حمل و دستی که برای کارهای سبک و کوچک مناسب هستند.
- دریلهای ستونی (Bench Drills): ماشینآلات ثابت و قوی که برای کارهای سنگینتر و دقیقتر استفاده میشوند.
- ماشینآلات CNC: ماشینآلات کنترل عددی کامپیوتری که دقت و سرعت بالایی دارند و برای تولید انبوه مناسب هستند.
مراحل سوراخکاری
۱-انتخاب ابزار مناسب: بسته به نوع ماده و اندازه سوراخ مورد نظر.
۲-نشانگذاری و اندازهگیری دقیق: برای تعیین محل دقیق سوراخ.
۳-ایجاد سوراخ اولیه: با استفاده از مته با قطر کوچکتر برای راهنمایی.
۴-گشاد کردن سوراخ: با استفاده از مته با قطر نهایی.
۵-پرداخت نهایی: برای از بین بردن لبهها و بهبود کیفیت سطح داخلی سوراخ.
اهمیت و کاربردها
سوراخکاری در صنایع مختلفی کاربرد دارد، از جمله:
- صنعت خودروسازی: برای مونتاژ قطعات موتور و بدنه.
- صنعت هوافضا: برای ایجاد سوراخهای دقیق در قطعات هواپیما.
- صنعت الکترونیک: برای ایجاد سوراخهای ریز در بردهای مدار چاپی.
- صنعت پزشکی: برای ساخت ابزارهای جراحی و قطعات دقیق.
- صنعت پایپینگ: برای نصب اتصالات و تجهیزات، تعمیر و نگهداری، انجام آزمایشات و …
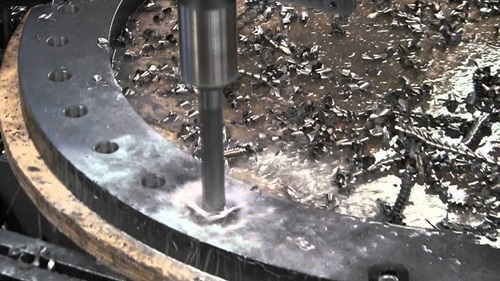
در این مقاله به دلیل اهمیت ویژه پایپینگ به بررسی دقیق تر سوراخکاری در این صنعت پرداخته می شود.سوراخکاری در صنعت پایپینگ در چندین موقعیت مختلف و برای اهداف مختلف بکار میرود. در اینجا به برخی از کاربردهای اصلی آن اشاره میکنم:
نصب اتصالات و تجهیزات
- نصب فلنجها: سوراخکاری برای نصب فلنجها به لولهها، که برای اتصال لولهها به یکدیگر یا به تجهیزات دیگر استفاده میشود.
- نصب شیرآلات: ایجاد سوراخهایی برای نصب شیرها و سایر تجهیزات کنترلی.
- نصب سنسورها و ابزارهای اندازهگیری: سوراخکاری برای نصب سنسورها، ترموکوپلها و سایر ابزارهای اندازهگیری و کنترلی.
اتصال لولهها
- برش و سوراخکاری لولهها: در مواقعی که نیاز به ایجاد اتصالات بین لولهها یا تغییرات در مسیر جریان مایع یا گاز داریم، از سوراخکاری استفاده میشود.
تعمیر و نگهداری
- بازرسی و تشخیص: ایجاد سوراخهایی برای بازرسی داخلی لولهها و تشخیص مشکلات مانند خوردگی یا ترکخوردگی.
- دسترسی به بخشهای داخلی: برای دسترسی به بخشهای داخلی لولهها برای تعمیرات و نگهداری.
کنترل جریان و تهویه
- پخش و جمعآوری جریان: سوراخکاری برای نصب اتصالاتی که به توزیع یکنواخت جریان یا جمعآوری آن کمک میکند.
- تهویه: ایجاد سوراخهایی برای تهویه یا تخلیه فشار اضافی در سیستم.
پیوستگی سیستمهای لولهکشی
- اتصال به سیستمهای دیگر: سوراخکاری برای ایجاد اتصالات به سیستمهای لولهکشی دیگر یا تجهیزات جانبی.
آزمایش و بررسی
- آزمایش فشار: سوراخکاری برای نصب اتصالات تست فشار و انجام آزمایشهای عملکردی.
نکات کلیدی در سوراخکاری در پایپینگ
- بررسی دقت: مهم است که سوراخها به دقت و با ابعاد مناسب ایجاد شوند تا از مشکلات در اتصال و عملکرد جلوگیری شود.
- توجه به ایمنی: استفاده از تجهیزات ایمنی و رعایت استانداردهای صنعتی برای جلوگیری از خطرات و آسیبها.
- انتخاب ابزار مناسب: بسته به نوع ماده لوله و نیاز پروژه، ابزار و روش مناسب برای سوراخکاری انتخاب شود.
در کل، سوراخکاری در پایپینگ یکی از فرآیندهای اساسی است که به نصب و نگهداری صحیح سیستمهای لولهکشی کمک میکند و باید با دقت و توجه به استانداردهای صنعتی انجام شود.
روشها و ابزارهای سوراخکاری در پایپینگ
- متههای دستی و برقی: برای سوراخکاری در مقیاس کوچک و در مواقعی که نیاز به دقت بالا نیست.
- دستگاههای برش لیزری: برای سوراخکاری در لولههای ضخیم یا مواد سخت با دقت بالا.
- واترجت: برای سوراخکاری در لولههای فلزی یا مواد سخت که به دقت و کیفیت بالا نیاز دارد.
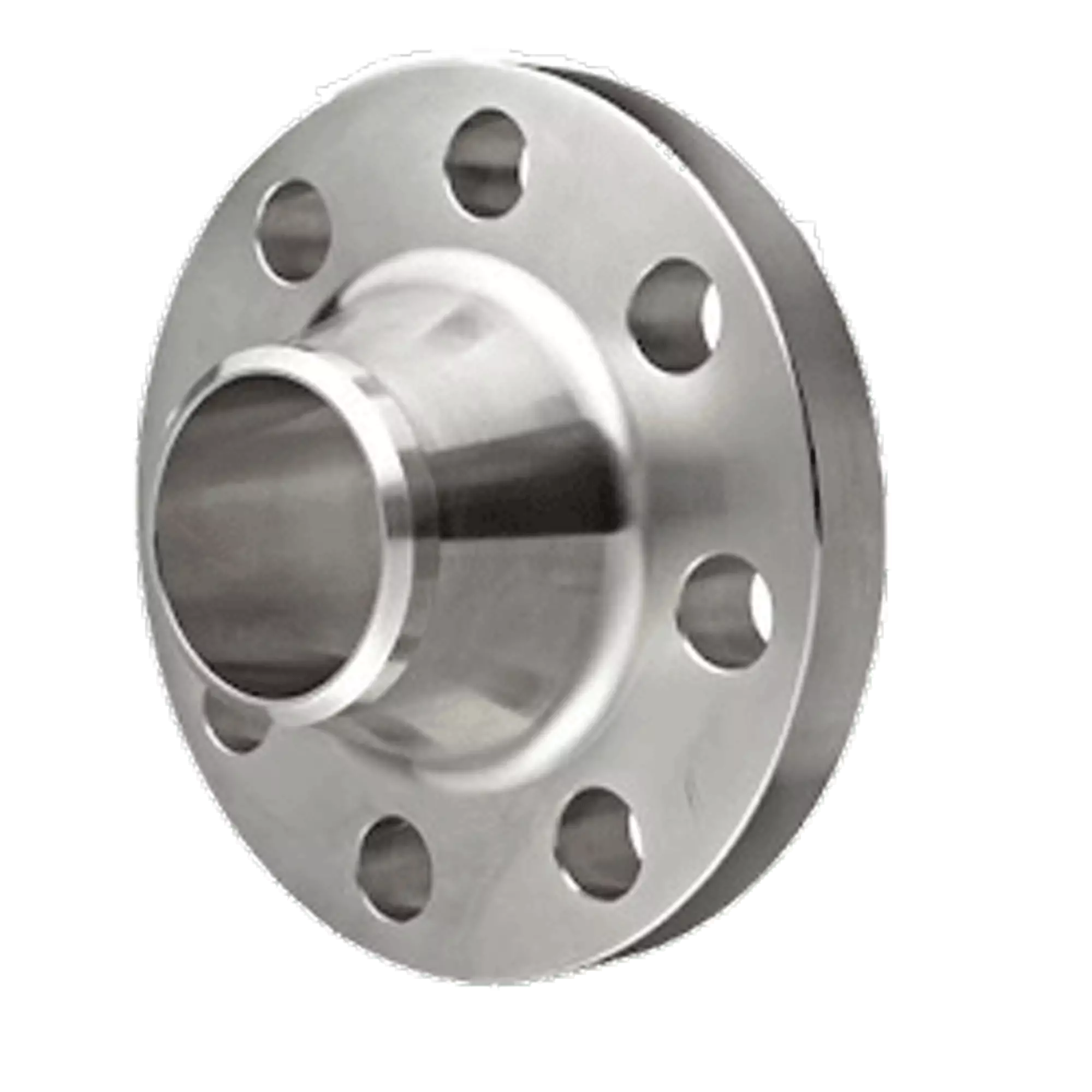
خرید اینترنتی فلنج
در بخش دوم این مقاله به بررسی استانداردهای مربوط به سوراخکاری پرداخته می شود. سوراخکاری یکی از فرایندهای مهم در مهندسی مکانیک و تولید صنعتی است و استانداردهای متعددی برای این فرایند وجود دارد که به کمک آنها میتوان دقت و کیفیت کار را تضمین نمود. این استانداردها شامل مواردی نظیر اندازهگیری، تلرانسها، روشهای اجرای عملیات و ایمنی میباشد. در زیر به برخی از مهمترین استانداردهای سوراخکاری اشاره میشود:
- استانداردهای ملی و بینالمللی
ISO 230-1: این استاندارد مربوط به ارزیابی دقت دستگاههای ماشینکاری است و به ویژه برای دستگاههای سوراخکاری مورد استفاده قرار میگیرد.
ANSI B94.11M: استانداردی آمریکایی که مشخصات فنی متهها و ابزارهای سوراخکاری را تعیین میکند.
DIN 338: استاندارد آلمانی برای متههای مارپیچ و ویژگیهای آنها.
- استانداردهای طراحی سوراخ
ISO 286-1: این استاندارد ابعاد و تلرانسهای مجاز برای سوراخها و شفتها را تعیین میکند.
ASME B1.1: استانداردی برای طراحی و ساخت پیچها و مهرهها که شامل ابعاد سوراخهای مناسب برای این قطعات میشود.
- استانداردهای فرآیند سوراخکاری و تلرانسی
ISO 1101: این استاندارد مربوط به تلرانسهای هندسی است و شامل دستورالعملهایی برای دقت سوراخها در فرآیند ماشینکاری میشود.
ISO 2692: استانداردی برای تلرانسهای موقعیتی سوراخها که در مونتاژ قطعات اهمیت دارد.
- استانداردهای روشهای سوراخکاری
ISO 9001: استاندارد مدیریت کیفیت که در تمام مراحل تولید از جمله سوراخکاری به کار میرود.
ISO 14001: استاندارد مدیریت محیط زیستی که در فرآیندهای تولید باید رعایت شود.
- استانداردهای ایمنی و محیط کار
OSHA (29 CFR 1910.212): استانداردهای ایمنی و حفاظت ماشینآلات در محیط کار که شامل دستگاههای سوراخکاری نیز میشود.
ISO 14001: استاندارد مدیریت محیط زیستی که میتواند شامل مدیریت پسماندهای تولیدی از فرآیند سوراخکاری باشد.
ISO 45001: استاندارد سیستم مدیریت ایمنی و بهداشت شغلی.
- استانداردهای ابزارهای سوراخکاری
ISO 15488: این استاندارد مربوط به متههای مخصوص و ویژگیهای آنهاست.
ISO 3299: استاندارد برای متههای پیچشی و مشخصات آنها.
ISO 3294: استانداردی برای ابزارهای کاربیدی که در سوراخکاری استفاده میشوند.
DIN 338: استاندارد آلمانی برای متههای پیچشی.
- استانداردهای مواد و پوششهای ابزارها
ISO 4957: استاندارد برای فولادهای ابزار که برای ساخت متهها استفاده میشود.
ISO 2081: استاندارد برای پوششهای الکتروپلیتینگ (مثلاً کروم) که ممکن است برای ابزارهای سوراخکاری استفاده شود.
- استانداردهای خاص ماشینآلات
ISO 230 : استاندارد برای آزمونهای ماشینابزارها که شامل دقت و قابلیت تکرار ماشینآلات سوراخکاری نیز میشود.
DIN 69063: استاندارد آلمانی برای ماشینآلات سوراخکاری.
- استانداردهای کیفیت و بازرسی
ISO 9001: استاندارد سیستمهای مدیریت کیفیت که برای تضمین کیفیت در فرآیندهای تولیدی از جمله سوراخکاری استفاده میشود.
ISO 10303 (STEP): استانداردی برای تبادل دادههای محصول، شامل اطلاعات مربوط به فرآیند سوراخکاری.
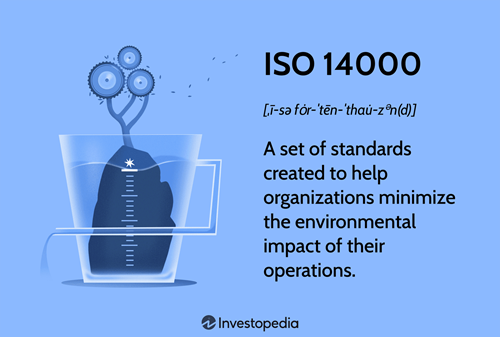
نکات کاربردی
- انتخاب ابزار مناسب: برای هر نوع ماده و اندازه سوراخ، انتخاب ابزار مناسب با استانداردهای مشخص شده اهمیت زیادی دارد.
- تنظیمات دستگاه: دستگاههای سوراخکاری باید مطابق با استانداردهای تعیین شده تنظیم و کالیبره شوند.
- کنترل کیفیت: پس از انجام عملیات سوراخکاری، باید بازرسیهای دقیق بر اساس استانداردهای کیفیت انجام شود تا اطمینان حاصل شود که سوراخها با مشخصات مورد نظر مطابقت دارند.
این استانداردها به عنوان راهنماهای جامعی برای انجام دقیق و کارآمد عملیات سوراخکاری به کار میروند و میتوانند در بهبود کیفیت و کاهش خطاها موثر باشند.
نتیجه گیری:
سوراخکاری یکی از فرآیندهای حیاتی و پرکاربرد در تولید و مهندسی مکانیک است که برای ایجاد سوراخهای دقیق و با کیفیت در مواد مختلف به کار میرود. این فرآیند با استفاده از ابزارهای مختلف مانند متهها انجام میشود و شامل انواع مختلفی مانند سوراخکاری معمولی، عمیق، ریز، زاویهدار و پلهای است که هر کدام برای کاربردهای خاصی مناسب هستند.
ابزارهای مورد استفاده در سوراخکاری نیز متنوع هستند و شامل متههای پیچشی، کاربیدی، تفنگی و پلهای میشوند. همچنین ماشینآلات مختلفی از جمله دریلهای دستی، ستونی و ماشینآلات CNC برای انجام عملیات سوراخکاری به کار میروند.
مراحل سوراخکاری شامل انتخاب ابزار مناسب، نشانگذاری و اندازهگیری دقیق، ایجاد سوراخ اولیه، گشاد کردن سوراخ و پرداخت نهایی است. این مراحل برای تضمین دقت و کیفیت سوراخها ضروری هستند.
سوراخکاری در صنایع مختلفی از جمله خودروسازی، هوافضا، الکترونیک و پزشکی کاربرد دارد و استانداردهای متعددی برای این فرآیند وجود دارد که به تضمین دقت و کیفیت کار کمک میکنند. این استانداردها شامل استانداردهای ملی و بینالمللی، طراحی سوراخ، فرآیند سوراخکاری، روشهای سوراخکاری، ایمنی و محیط کار، ابزارهای سوراخکاری، مواد و پوششهای ابزارها، ماشینآلات و کیفیت و بازرسی هستند.
استفاده از این استانداردها در فرآیند سوراخکاری به بهبود کیفیت، افزایش دقت و کاهش خطرات ایمنی کمک میکند و به عنوان راهنماهای جامعی برای انجام دقیق و کارآمد عملیات سوراخکاری به کار میروند.