ابزار دقیق شاخهای از مهندسی است که به اندازهگیری و کنترل کمیتهای مختلف در فرآیندهای صنعتی و علمی میپردازد. این کمیتها میتوانند شامل فشار، دما، سطح مایعات، جریان، سرعت و بسیاری دیگر باشند. هدف اصلی ابزار دقیق، دستیابی به دقت بالا در اندازهگیری و کنترل فرآیندها است.
ابزار دقیق از سه بخش اصلی شامل سنسور یا دستگاه ورودی، پردازشگر سیگنال و گیرنده یا دستگاه خروجی تشکیل شده است.
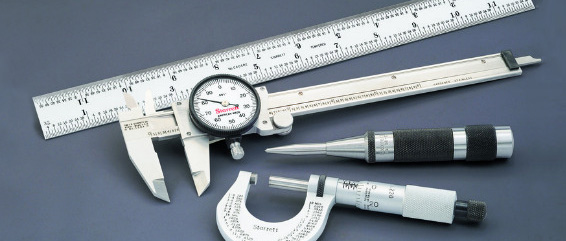
اجزای اصلی ابزار دقیق
- حسگرها (Sensors): وظیفه تشخیص و اندازهگیری کمیتهای فیزیکی را دارند و این کمیتها را به سیگنالهای الکتریکی تبدیل میکنند.
- ترانسمیترها (Transmitters): سیگنالهای دریافتی از حسگرها را تقویت و به واحدهای کنترل ارسال میکنند.
- کنترلرها (Controllers): سیگنالهای ورودی را تحلیل و پردازش میکنند و براساس آن تصمیمگیریهای لازم برای تنظیم فرآیندها را انجام میدهند.
- عملگرها (Actuators): دستورات صادره از کنترلرها را به عمل مکانیکی تبدیل میکنند، مانند باز و بسته کردن شیرها یا تنظیم میزان جریان.
- نمایشگرها و رکوردرها (Indicators and Recorders): اطلاعات و دادههای مربوط به فرآیندها را نمایش میدهند و ثبت میکنند.
کاربردها
- صنایع نفت و گاز: برای کنترل فرآیندهای استخراج، پالایش و توزیع.
- صنایع شیمیایی: برای کنترل واکنشهای شیمیایی و تولید محصولات.
- صنایع غذایی و دارویی: برای حفظ کیفیت و بهداشت محصولات.
- نیروگاهها: برای کنترل تولید و توزیع انرژی.
- هوا و فضا: برای کنترل سیستمهای پروازی و فضایی.
مزایا
- افزایش دقت و صحت در اندازهگیریها
- بهبود کیفیت محصولات و فرآیندها
- کاهش هزینهها و افزایش بهرهوری
- افزایش ایمنی در فرآیندهای صنعتی
ابزار دقیق با توجه به کاربردهای گسترده و اهمیت بالایی که در صنایع مختلف دارد، نقش بسیار حیاتی در بهبود و توسعه فرآیندهای صنعتی و علمی ایفا میکند.
ابزار دقیق در صنعت پایپینگ نقش حیاتی در کنترل و نظارت بر فرآیندهای انتقال مایعات و گازها دارد. این ابزارها به منظور اندازهگیری و کنترل فشار، جریان، دما، سطح مایعات و دیگر پارامترهای مهم در سیستمهای لولهکشی به کار میروند. در زیر به برخی از کاربردها و اجزای ابزار دقیق در صنعت پایپینگ اشاره میکنم:
کاربردهای ابزار دقیق در پایپینگ
- اندازهگیری فشار: فشارسنجها (مانومترها) برای اندازهگیری فشار داخلی لولهها استفاده میشوند. این دستگاهها میتوانند از نوع مکانیکی یا الکترونیکی باشند.
- اندازهگیری جریان: جریانسنجها (فلومترها) برای اندازهگیری نرخ جریان مایعات و گازها در لولهها به کار میروند. انواع مختلفی از جریانسنجها وجود دارند، مانند جریانسنجهای مغناطیسی، توربینی و اولتراسونیک.
- اندازهگیری دما: ترموکوپلها و RTDها برای اندازهگیری دمای مایعات و گازها در لولهها استفاده میشوند.
- اندازهگیری سطح: سطحسنجها برای اندازهگیری سطح مایعات در مخازن و لولهها به کار میروند.
- کنترل جریان و فشار: شیرهای کنترلی و رگولاتورها برای تنظیم و کنترل جریان و فشار در سیستمهای لولهکشی استفاده میشوند.
- نظارت و کنترل از راه دور: سیستمهای اسکادا (SCADA) و DCS برای نظارت و کنترل فرآیندهای لولهکشی از راه دور به کار میروند.
صدور پیشفاکتور آنلاین
ابزار دقیق در صنعت پایپینگ با فراهم کردن دقت بالا در اندازهگیری و کنترل پارامترهای مهم، نقش کلیدی در بهبود کارایی و ایمنی سیستمهای لولهکشی دارد.
حال پس از توضیح کلی ابزار دقیق و تشریح کاربرد آن در صنعت پایپینگ، در این بخش توضیحات کاملی از نحوه کنترل و اندازه گیری یک کمیت که فرایند پایه در ابزار دقیق می باشد، ارائه شده است:
برای کنترل و اندازهگیری یک کمیت، معمولاً سیگنالی که مقدار مورد نظر را نشان میدهد، به یک دستگاه که وظیفهی نشان دادن یا پردازش اطلاعات را بر عهده دارد، ارسال میشود. اگر کنترل بهصورت خودکار انجام شود، رایانه سیگنالی به دستگاه کنترل نهایی میفرستد که سپس بر کمیت اندازهگیری شده تأثیر میگذارد.
کمیتهایی که معمولاً اندازهگیری میشوند شامل دما، فشار، سرعت، جریان، نیرو، حرکت، شتاب، تنش، کرنش، سطح یا عمق، جرم، وزن، چگالی، اندازه یا حجم و اسیدیته/قلیایی هستند.
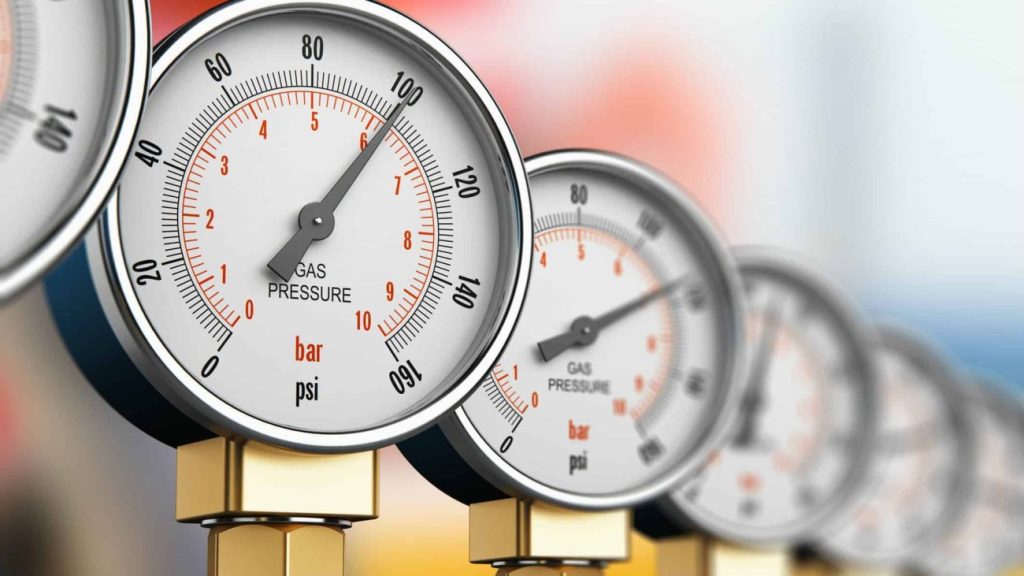
رایج ترین اصطلاحات و تعاریف فرآیند کنترل شامل موارد زیر است:
فرایند (Process): به مجموعهای از فعالیتها یا عملیاتهایی گفته میشود که در یک سیستم یا واحد صنعتی برای تبدیل مواد اولیه به محصولات نهایی یا انجام یک عملکرد مشخص انجام میشود. این فرایندها میتوانند شامل مراحل مختلفی باشند و معمولاً شامل اندازهگیری، کنترل، و تنظیم پارامترهای مختلف برای بهینهسازی عملکرد سیستم در ابزار دقیق هستند.
Process Variable (PV) : به متغیری اطلاق میشود که مقدار آن نمایانگر وضعیت یک فرایند در سیستم صنعتی است. این متغیر میتواند هر چیزی باشد که نیاز به نظارت و کنترل دارد، مانند دما، فشار، جریان، سطح مایع، و یا دیگر پارامترهای فرآیند.
Setpoint (نقطه تنظیم): مقداری است که در آن یک متغیر فرآیند باید حفظ شود. به عبارت دیگر، مقدار “هدف” برای متغیر فرآیند است.
Transducer (مبدل): یک دستگاه حیاتی است که نقش کلیدی در تبدیل سیگنالها بین انواع مختلف انرژیها دارد. در این زمینه، ترانسدیوسرها به طور خاص برای تبدیل مقادیر فیزیکی یا شیمیایی به سیگنالهای الکتریکی و برعکس، استفاده میشوند. این فرآیند تبدیل برای نظارت، کنترل و تنظیم فرآیندهای صنعتی بسیار ضروری است.
Primary Sensing Element (عنصر حسگر اولیه): اولین قسمت از یک سیستم اندازهگیری است که به طور مستقیم با متغیر فیزیکی یا شیمیایی مورد نظر در تماس است و آن را حس میکند. این عنصر وظیفه دارد تا اطلاعات اولیه را از محیط اطراف به شکل قابل اندازهگیری دریافت کند و سپس این اطلاعات را به سیگنالهایی تبدیل کند که میتوانند توسط سایر اجزای سیستم پردازش شوند.
Transmitter (ترانسمیتر): دستگاهی است که وظیفه اصلی آن تبدیل و ارسال سیگنالهای اندازهگیریشده به شکل قابل استفاده و قابل انتقال به سیستمهای کنترل یا نمایشگرها است. ترانسمیترها نقش مهمی در ارتباط بین عناصر حسگر (PSE) و سیستمهای کنترل یا نمایش اطلاعات دارند.
Lower Range Value & Upper Range Value (مقادیر پایین و بالای محدوده): به مقادیر مرجع اطلاق میشوند که برای تنظیم و کالیبراسیون دستگاههای اندازهگیری و کنترل به کار میروند. این مقادیر برای تعریف دامنه اندازهگیری دستگاهها و تعیین نقطه شروع و پایان مقیاس آنها استفاده میشوند.
Zero: به نقطهای اشاره دارد که در آن دستگاه باید با مقدار صفر تنظیم شود. در واقع، صفر به عنوان نقطه مرجع برای اندازهگیریهای دستگاه عمل میکند. تنظیم صحیح صفر برای دقت و صحت اندازهگیری بسیار مهم است.
Span: به دامنه یا فاصله بین مقدار صفر و مقدار بالای اندازهگیری دستگاه اشاره دارد.Span نشاندهنده گسترهای است که دستگاه میتواند به طور صحیح اندازهگیری کند و معمولاً به عنوان تفاوت بین Lower Range Value & Upper Range Value تعریف میشود.
Controller (کنترل کننده) : دستگاهی است که برای مدیریت و تنظیم فرآیندها در سیستمهای صنعتی استفاده میشود. هدف اصلی کنترلرها این است که پارامترهای مشخصی (مانند دما، فشار، جریان، سطح، و غیره) را در محدوده مطلوب نگه دارند تا فرآیند بهینه و پایدار باقی بماند.
Final Control Element (عنصر نهایی کنترل): به آخرین بخش از یک سیستم کنترل اطلاق میشود که مستقیماً بر روی فرآیند فیزیکی تاثیر میگذارد. این عنصر وظیفه دارد تا بر اساس سیگنالهای کنترلی دریافتی از کنترلر، تغییرات لازم را در فرآیند اعمال کند. به عبارت دیگر، عنصر نهایی کنترل به اجرای دستورات کنترلی صادر شده توسط کنترلر پرداخته و تغییرات فیزیکی را در فرآیند اعمال میکند.
Manipulated Variable (متغیر دستکاری شده): به پارامتری اشاره دارد که توسط سیستم کنترل به طور عمدی تغییر داده میشود تا تأثیر لازم بر روی متغیر فرایند را ایجاد کند و آن را به نقطه تنظیم (Set Point) نزدیک کند. این متغیر به عنوان ورودی به سیستمهای کنترلی عمل کرده و مستقیماً بر فرآیند تاثیر میگذارد.
Automatic Mode (حالت اتوماتیک) : در ابزار دقیق به حالتی اطلاق میشود که در آن سیستم کنترل بدون نیاز به مداخله دستی از سوی اپراتور، بهطور خودکار پارامترهای فرآیند را نظارت و تنظیم میکند. این حالت به سیستم اجازه میدهد که به طور پیوسته و خودکار فرآیندها را کنترل کرده و به وضعیتهای مطلوب برسد، بهویژه در شرایطی که تغییرات فرآیند نیاز به واکنش سریع دارد.
Manual Mode (حالت دستی): در ابزار دقیق به حالتی اشاره دارد که در آن کنترل فرآیندها و تنظیمات به صورت دستی توسط اپراتور انجام میشود، به جای اینکه به طور خودکار توسط سیستم کنترل مدیریت شود. در این حالت، اپراتور مسئولیت نظارت بر پارامترهای فرآیند و اعمال تغییرات مورد نیاز را به عهده دارد.
International Society of Automation (انجمن بین المللی اتوماسیون): سازمانی معتبر در زمینه ابزار دقیق و اتوماسیون صنعتی است. این سازمان استانداردها و دستورالعملهایی را برای بهبود کارایی و دقت در سیستمهای ابزار دقیق و اتوماسیون ارائه میدهد.
Tag Numbers: شمارههای شناسایی در ابزار دقیق، به عنوان شناسههای منحصر به فرد برای ابزارها و تجهیزات در سیستمهای کنترل و نظارت صنعتی عمل میکنند. این شمارهها به سازماندهی، شناسایی و مدیریت مؤثر تجهیزات کمک میکنند و اطلاعات مربوط به عملکرد و وضعیت آنها را به راحتی در دسترس قرار میدهند.
Alarm (هشدار): به سیگنال یا پیامی اطلاق میشود که برای اطلاعرسانی در مورد وضعیت غیرعادی یا خطرناک در یک فرآیند یا سیستم کنترل به کار میرود. هدف از سیستمهای هشدار، فراهم کردن زمان و اطلاعات کافی برای اپراتورها و تکنسینها برای اقدام به موقع جهت جلوگیری از مشکلات جدی، آسیب به تجهیزات یا وقوع حوادث است.
Binary : به سیستمی از نمایش دادهها اشاره دارد که تنها از دو وضعیت یا حالت ممکن استفاده میکند: ۰ و ۱. این مفهوم در بسیاری از جنبههای ابزار دقیق، از جمله کنترل، نظارت، و انتقال دادهها، کاربرد دارد.
Balloon : معمولاً به نوعی از تجهیزات یا ابزارها اشاره دارد که به صورت فیزیکی شبیه به بالون یا بادکنک هستند و برای اندازهگیری، کنترل یا تنظیم فشار استفاده میشوند. این اصطلاح میتواند به اشکال مختلفی از دستگاهها و ابزارها اطلاق شود.
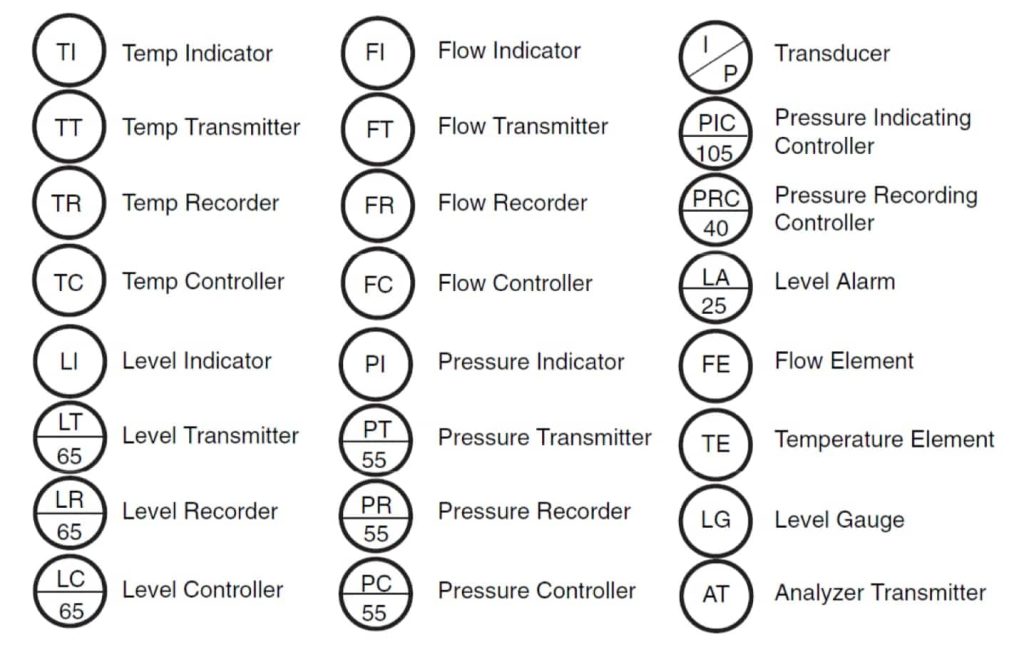
در انتها به بررسی وظایف مهندس ابزار دقیق پرداخته می شود:
مهندس ابزار دقیق نقشی بسیار حیاتی در صنایع مختلف ایفا میکند. ارزش کار این مهندسین را میتوان در چندین جنبه بررسی کرد:
- دقت و کنترل کیفیت: مهندس ابزار دقیق مسئول نصب، تنظیم، و نگهداری ابزارهای اندازهگیری و کنترل است. این ابزارها برای اطمینان از کیفیت محصول و عملکرد صحیح سیستمها ضروری هستند. بدون دقت در این اندازهگیریها، محصولات ممکن است به درستی تولید نشوند یا سیستمها به درستی کار نکنند.
- بهینهسازی عملکرد: مهندس ابزار دقیق میتواند با استفاده از دادههای جمعآوری شده توسط ابزارهای دقیق، عملکرد سیستمها را تحلیل و بهینهسازی کند. این بهبود عملکرد میتواند منجر به افزایش بهرهوری و کاهش هزینهها شود.
- پیشگیری از خرابی: با نظارت مداوم و دقیق بر عملکرد تجهیزات، مهندس ابزار دقیق میتواند مشکلات را قبل از اینکه به خرابیهای جدی تبدیل شوند، شناسایی کند. این کار به کاهش زمانهای توقف غیرمنتظره و هزینههای تعمیرات کمک میکند.
- ایمنی: ابزارهای دقیق میتوانند برای نظارت بر شرایط ایمنی در صنایع مختلف استفاده شوند. مهندس ابزار دقیق مسئول اطمینان از اینکه این ابزارها به درستی کار میکنند و به ایمنی کارکنان و محیط کمک میکنند، است.
- پشتیبانی از نوآوری و فناوری: مهندسان ابزار دقیق در فرآیندهای تحقیق و توسعه نقش مهمی دارند. آنها میتوانند به پیادهسازی فناوریهای جدید و بهبود روشهای موجود کمک کنند.
در کل، ارزش کار یک مهندس ابزار دقیق در توانایی او برای اطمینان از دقت، بهینهسازی عملکرد، پیشگیری از خرابی، حفظ ایمنی، و حمایت از نوآوری در صنایع مختلف است.
نتیجه گیری:
ابزار دقیق در مهندسی به اندازهگیری و کنترل کمیتهای مختلف در فرآیندهای صنعتی و علمی پرداخته و از سه بخش اصلی شامل حسگرها، ترانسمیترها و کنترلرها تشکیل شده است. این ابزارها با دقت بالا در اندازهگیری و کنترل پارامترهایی مانند فشار، دما، جریان و سطح مایعات، نقش اساسی در بهبود کیفیت، ایمنی، و بهرهوری فرآیندها دارند.
در صنعت پایپینگ، ابزار دقیق برای نظارت و کنترل بر روی فرآیندهای انتقال مایعات و گازها استفاده میشود و شامل اجزای مختلفی مانند حسگرها، ترانسمیترها، و شیرهای کنترلی است. کاربردهای این ابزارها در پایپینگ شامل اندازهگیری فشار، جریان، دما و سطح مایعات، و همچنین کنترل از راه دور میشود.
مهندس ابزار دقیق نقش کلیدی در اطمینان از دقت اندازهگیریها، بهینهسازی عملکرد سیستمها، پیشگیری از خرابیها، حفظ ایمنی، و حمایت از نوآوری در صنایع دارد. وظایف او شامل نصب و نگهداری ابزارهای اندازهگیری، تحلیل دادهها، و نظارت بر عملکرد تجهیزات به منظور کاهش هزینهها و افزایش بهرهوری است.
در نهایت، ابزار دقیق بهعنوان یک حوزه تخصصی با کاربردهای گسترده در صنایع مختلف، اهمیت زیادی در بهبود فرآیندها و توسعه فناوریهای نوین دارد.